1 基准及辅助基准的选择、加工、标识
如果说图纸是工程的语言,那么图纸上的基准是加工和装配的路标,加工中心在加工零件时,首先必须在图纸上寻找基准,在通常状况下,零件须经过刨床加工、磨床加工2面后,才能进入CNC加工的。在确定基准时,通常状态下,零件上只要铣出一条基准边和一个基准孔或一个销孔或导柱孔,并在图纸上标识。操作工也可以在工件上做记号,以便于下一次返工,测量尺寸时做基准。然而对于复杂的三维曲面,通常都需要进行五面三维加工。底面进行销孔、键槽、螺丝孔的加工,所以我们引入辅助基准的概念。例如,要设计加工一个直径为?600mm的半球零件,半球要进行三维曲面加工,半球底面要加工键槽定位或用销孔定位及螺丝孔,如图1、图2所示,所以,在设计时,一定要另外多设计4个工艺柱子,加工时,4个工艺柱子与底面互为基准进行加工,然后再加工一块工装板,在工装板上加工一个基准边和一个基准孔(X800,Y0),同时在工装板上加工出相应的定位销孔和螺丝孔,这样才能把铸件锁在工装板上,就可以进行三维曲面加工了。该工装板的基准边,基准孔,应在图纸上标识,存档,当然。工装板也可以用下模板代替。
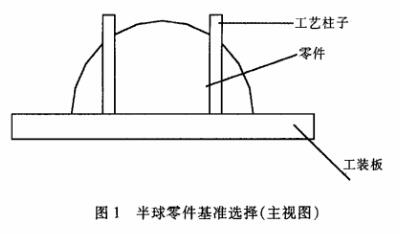
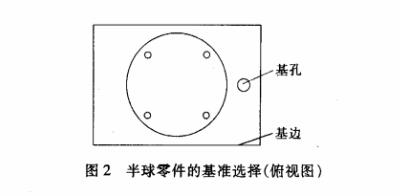
对于复杂曲面的零件来说,一个工位状态下进行三维加工是不能满足要求的,可能要进行3个工位,甚至6个工位才能完成三维加工。例如,加工摩托车油箱内壳拉伸模的凸模时,要用3个工位才能完成三维的加工。由于该零件尺寸长660mm,宽330mm,高320mm,如图3、图4、图5所示。这在一种工位上加工到位是不可能完成的,故需要加工一块工装板,在工装板上加工一个基准边和一个基准孔并加工与凸模上的螺丝孔、键槽或销孔相对应的孔,在图纸上进行标识,记录下基准孔的坐标,这样再进行A面(顶面)的三维加工,A面加工完后,在A面加工工位上铣出辅助基准E和H的尺寸并记录在图纸上,作为加工B面、C面时的对刀依据。在加工B面或C面时,必须先将角铁爬表看正并装夹在工作台上,将工件翻转90°,安装在角铁上。进行爬表,看正,校对X ,Y,Z的参考点,并把参考点基准转到固定物上,同时操作员要记录下来,以便让下一班操作人员知道加工基准,并进行校对。这样就能够防止交接班出现错误,提高生产率。
2 粗加工的程序编制应注意的几个问题
(1)编程人员在编程时应首先测量毛坯尺寸,使得定义毛坯尺寸与实物尺寸一样.这样就可以避免撞刀
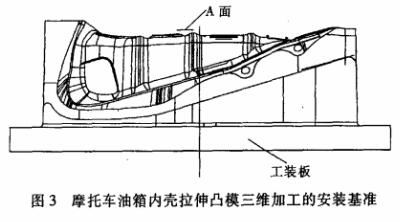
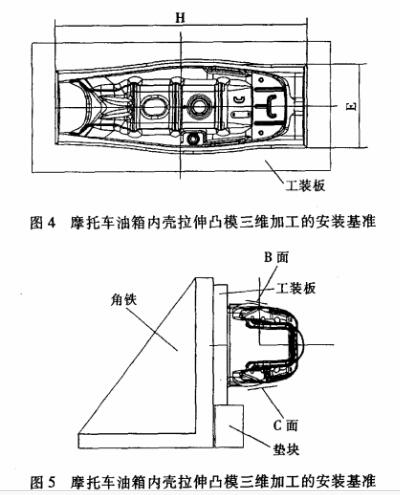
(2)在编制挖槽层切粗加工程序时用,采用螺旋下刀,每层切深0.8-1.0mm,若不用螺旋下刀(受空间限制),直接下刀要用2个进给速度,即Z轴进给150mm/min和X,Y进给1500-2000mm/min。如果用一个进给速度,很容易产生打刀。
(3)在编制挖凹槽粗加工程序时应注意:①安全高度的选择要正确,否则会产生打刀现象;②斜面很陡时,圆刀片接触面积较大,容易产生震动及嗓音,这时主轴转速要降低,每层切削深度约0.6mm左右,进给速度要相应变小。
(4)加工凸模,挖槽粗加工时,同时存在顺铣与逆铣.这样当深度铣到较深时,或加工到斜面坡度较大时,若逆铣声音较大.震动较大,在这不良加工状态下,建议停止加工,改变加工工艺,而采用等离外形加工,并限定深度进行单向顺铣切削,这样既好加工,又节省时间,延长刀具寿命,提高生产率。
(5)在编程切粗加工时,要注意选择好刀具刀径与间距的关系,程序编好后要进行实体模拟运行,检查程序是否有过切现象,同时观察每层层切是否加工到位,如果层切时刀间距太大,每层加工不干净,产生多余的台(柱)状,这样给下一刀层切加工带来困难,甚至会发生打刀现象,需要重新计算直到完好为止。
3 精加工编程加工应注意的几个问题
由于粗加工留下加工余量及受刀具的限制,粗加工大都采用PD40(R5mm)的刀具,精加工大部分用QT20、QT16、QT10等,局部小凹槽粗加工无法到位,留下余量较多,故在精加工之前,一定要先进行清根或半精加工,这样使得余里*均匀,不会产生局部余量太多而产生打刀现象。
在编制等高外形的精加工程序的过程中,编程人员若采用直接下刀,则在下刀处会产生过切现象。这对于精密模具来讲,是不可以的,故建议编程人员在编制等高外形的精加工时,一定要用进刀和退刀的方式导人,在定义下刀点时,在不重要的斜面上或在坡度较大的斜面下刀,这样加工出来的表面质量较好。对于局部小凹槽而言,也可能上述刀具精加工曲面不能加工到位,故必须用*小的刀具来定义切削范围,进行局部三维加工。
在编程加工中,若三维造型以凹模为准,则加工凹棋必须到位。加工凸模时,必须过切一个料厚,并在图纸上或在程序上加以标识。这样不会弄错,否则很容易发生错误,加工出来没有料厚,必须重新返工,影响模具交货期,这种现象不能发生。